ENGINEERING EXPERIENCE

NASA Space Grant Internship
2015 Summer Intern & 2016 Mentor
“Space Grant is a national network of colleges and universities. These institutions are working to expand opportunities for Americans to understand and participate in NASA's aeronautics and space projects by supporting and enhancing science and engineering education, research and public outreach efforts.”
Collaborated with a diverse team of engineers to successfully launch & test a near space ballooning data collection research project that observed the health of vegetation utilizing near-infrared spectroscopy.
Ran flight simulation programs to further design the size, weight and type of weather balloon to launch.
Personally managed multiple tasks from leading the structural analysis of the impact to the payload, to clearly documenting & presenting the design process, technical challenges & solutions for end of mission summary reports.
Programmed, tested, and assembled several Arduino microcontrollers with altimeters, gyroscopes, accelerometers & magnetometers to be used for data collection.
Designed & tested a homemade cut-down mechanism, utilizing Arduinos, for the glider to be released from the weather balloon at 400ft.
Conducted the near space balloon launch, successfully recovered the payload and analyzed all of post flight data.
Served as a mentor for the incoming interns for the next NASA weather balloon launch the following year after.
Gave various software and hardware workshops involving Arduino basics, breadboarding, SolidWorks, AutoCAD, Inventor and more.
Managed an entire team of undergraduate engineers, serving as a liaison between students, professors and lab managers.
Led outreach programs and booths at various city fairs, high schools and community colleges.
NASA Near Space Ballooning Launch Day Ground Footage
NASA Near Space Ballooning Launch Day Payload Footage

After weeks of preparation along with trial and error we worked as a team to finally launch our curated payload to successfully accomplish multiple mission requirements.
Our payload consisted of a homemade Arduino cutdown mechanism, various cameras for visual data collection & multiple sensors such as an altimeter, gyroscope, accelerometer & magnetometer for basic data collection.

Additionally we decided to add a fixed wing glider attached by a rope below our main payload to detach from 400ft with a goal of gliding through an area of vegetation. We modified a Canon camera to take in near-infrared light to observe the health of vegetation utilizing near-infrared spectroscopy and placed it within the glider itself to be used as a transportation vehicle.
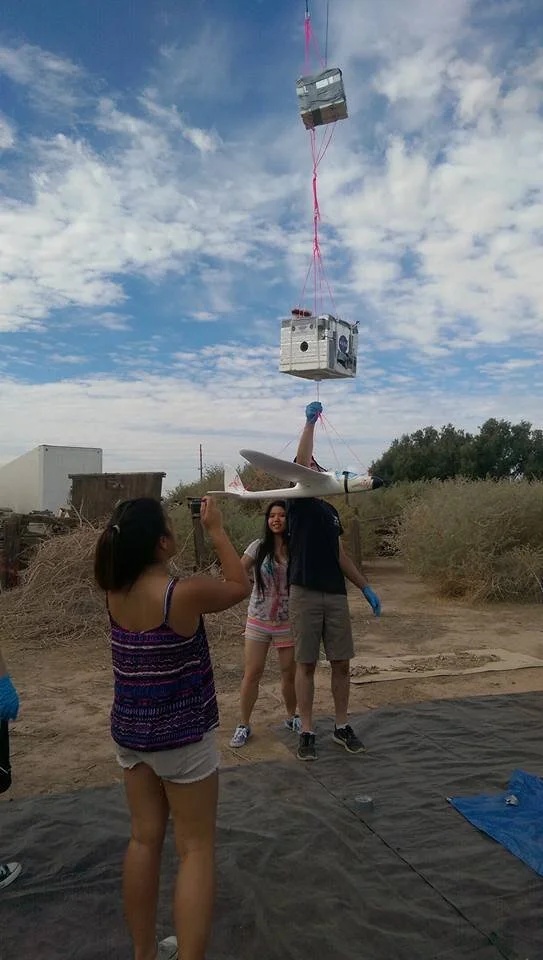
Our final release of the entire weather balloon along with our two payloads.
Our entire weather balloon payload system at launch. From top to bottom we have the weather balloon itself, parachute, cut down mechanism, main payload housing all sensors and cameras, and finally our fixed wing glider set to cut off at 400ft.
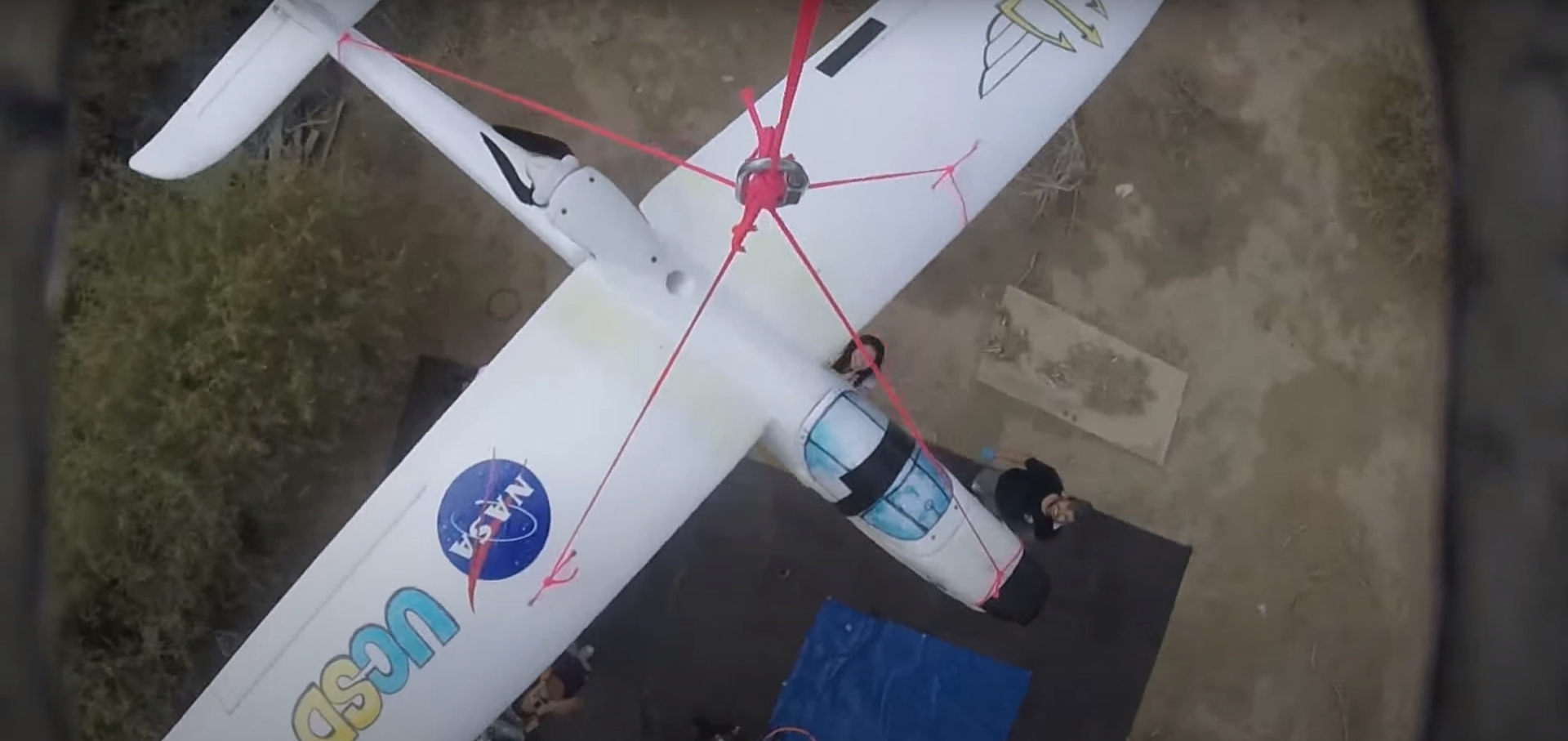
Photo from the bottom of the main payload of our aircraft attached, about 20ft above us.
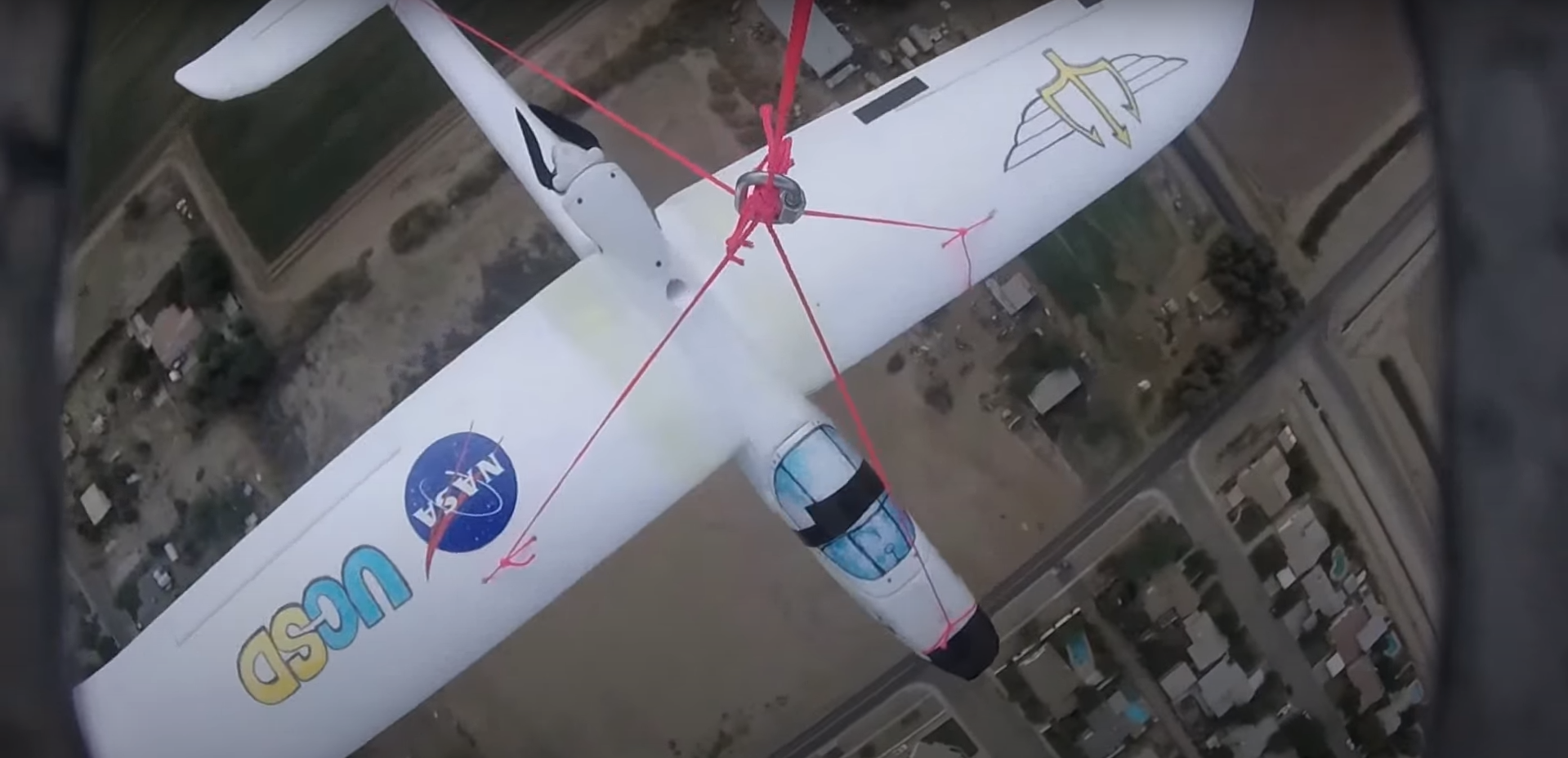
Photo from the bottom of the main payload of our aircraft attached, about 350ft above us, right before its intended descent.
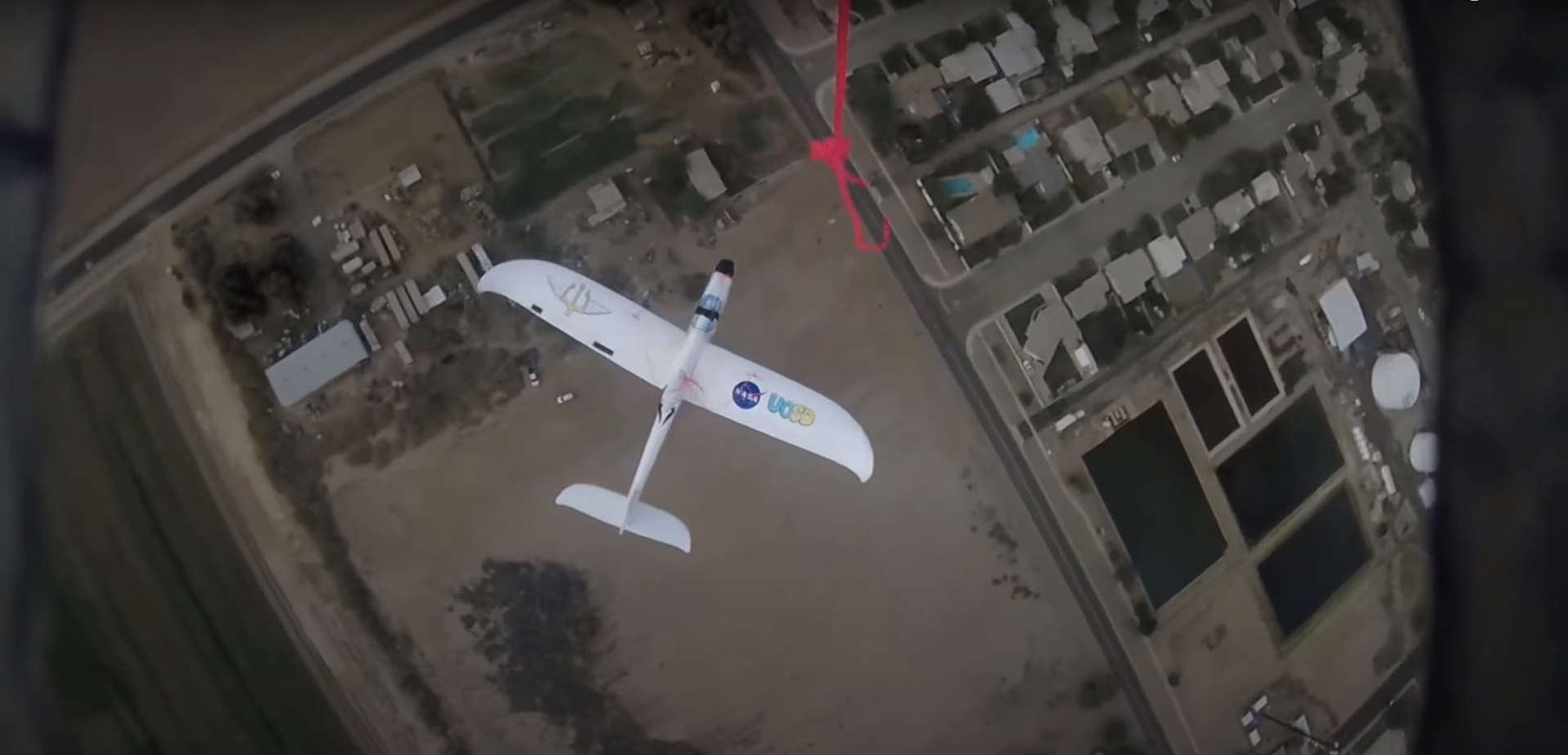
Photo from the bottom of the main payload of our aircraft detaching at 400ft, mission successful.
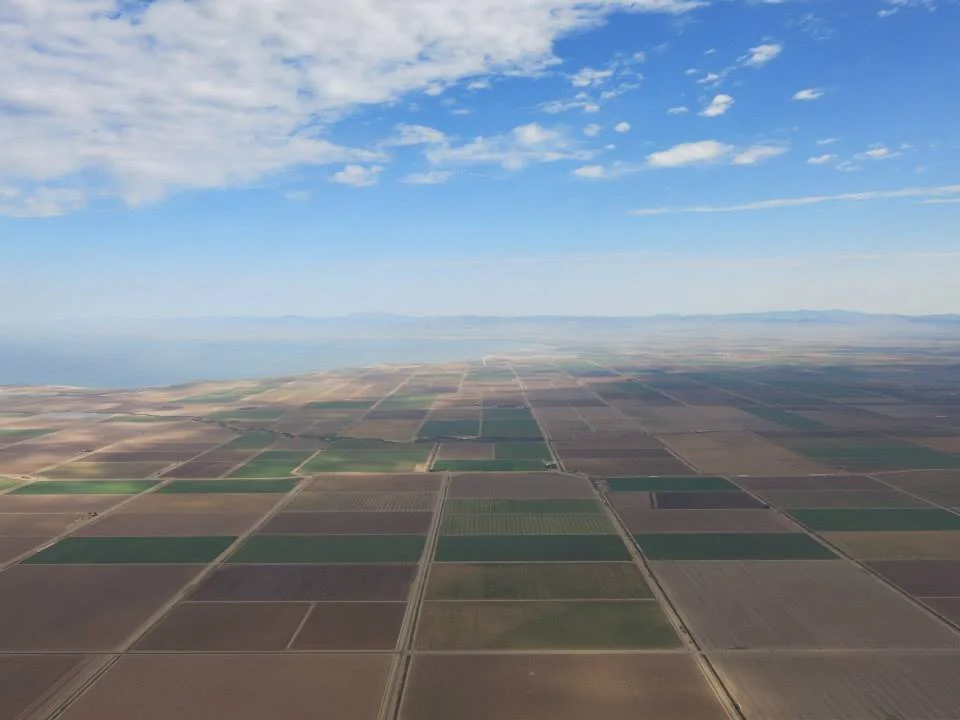
Photos taken by our preprogrammed cameras within the main payload.
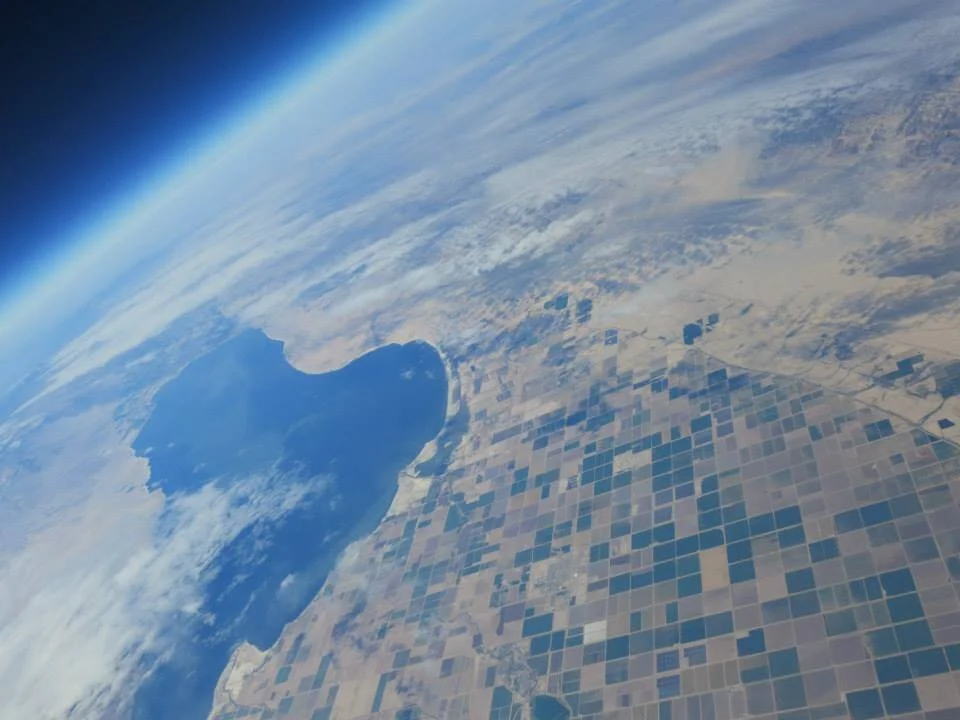
Photos taken by our preprogrammed cameras within the main payload.
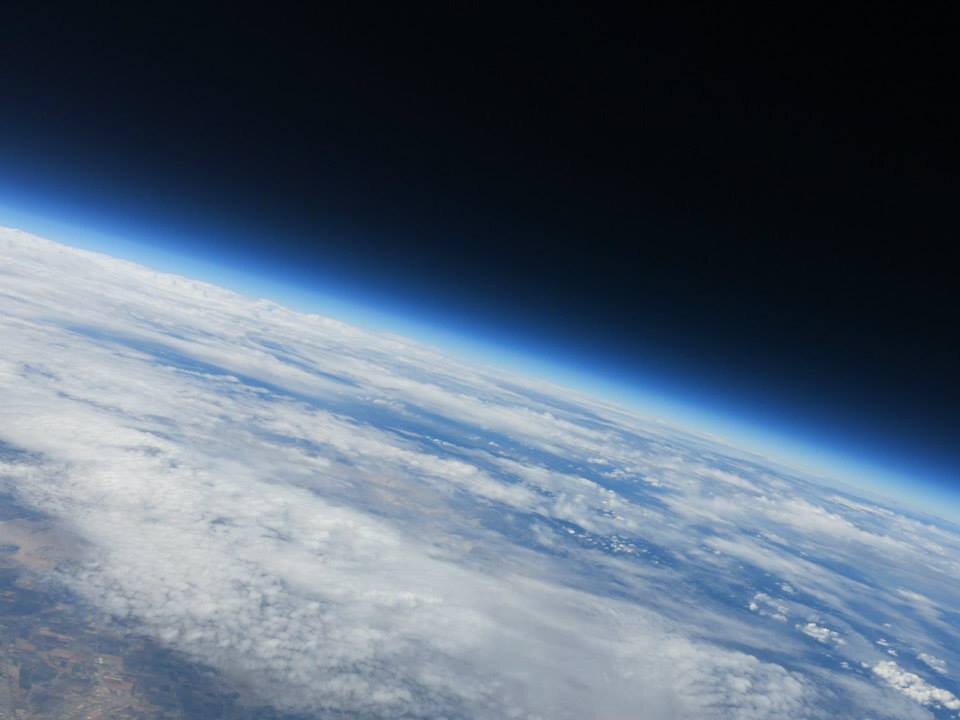
Photos taken by our preprogrammed cameras within the main payload.
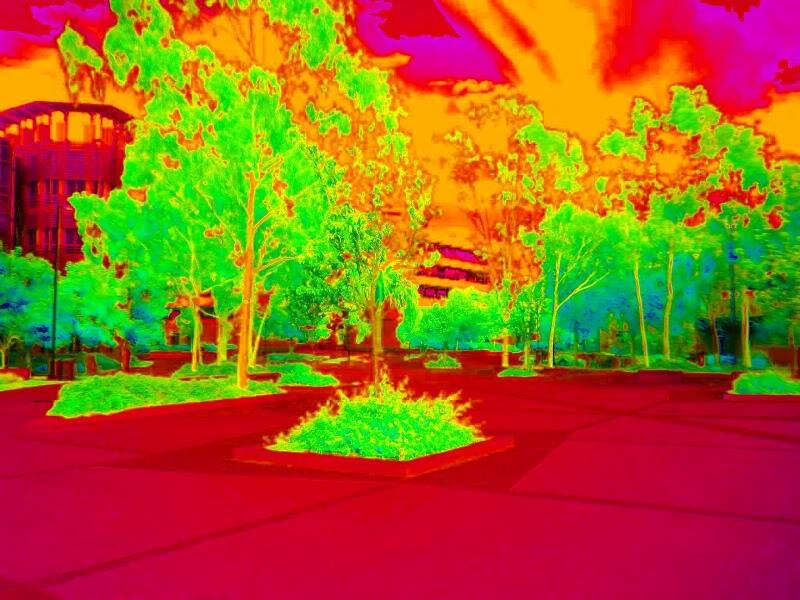
This is a photo during our testing phase of the deconstructed and reprogrammed Canon camera to take near-infrared photos of various types of vegetation to observe their health.

UCSD Senior Design, Build & Test Project
Development of an extended composite wing for long range silent surveillance flights
As part of a research project, we were requested to develop a composite wing, with a span of at least 6ft, that internally carried 20 lbs of LiPo batteries for extended surveillance, so that the new aircraft has a maximum take-off weight of 55 lbs which meets the new FAA FAR 107 weight limits. The 10 lbs of batteries per wing can be carried at any location.
Given the properties and performance of an existing 35 lb UAV with a composite wing, we had to redesign the wing for improved structural & cost performance.
Worked in a team of 11 aerospace structural engineers to fully design, build and test a 7.5' NACA-0012 carbon fiber wing that covered all necessary mission requirements while ensuring ideal cost performance.
Reviewed provided loads, available materials, environment & FAR/EASA requirements and iterated a wing design until all points were met.
Drafted and reviewed multiple hand calculations for preliminary design & analysis, running our design through multiple load cases.
Created numerous 2D drawings within AutoCAD to showcase the intended design of the wing in cross section & plan views.
Utilized SolidWorks to 3D model the entire wing design along with the tooling needed for fabrication of the physical wing.
Budgeted, ordered & organized all the necessary materials for the wing itself along with tools needed for fabrication.
Planned & detailed out the entire 6 week manufacturing schedule for the fabrication of the carbon fiber wing.
Ran FEA simulations on ABAQUS utilizing our 3D model to predict failure modes & loads.
Conducted multiple manufacturing methods including numerous wet lay-ups combined with pre-preg for the main spar, aft spar, wing skins, ribs and stringers.
Laser cut plywood and assembled 10 male tooling parts for the carbon fiber rib manufacturing process.
Installed strain gauges and built whiffle trees to successfully measure strain and apply loads during testing.
Assigned project schedule & milestones for the first 10 weeks.
Assigned project schedule & milestones for the last 10 weeks.
Key Performance Indicator Equation (KPI)
After several team meetings, discussions & analysis we finalized a wing design to achieve the project objective & requirements.
Utilizing our given loads we developed a composite layup plan to accompany our design wing.
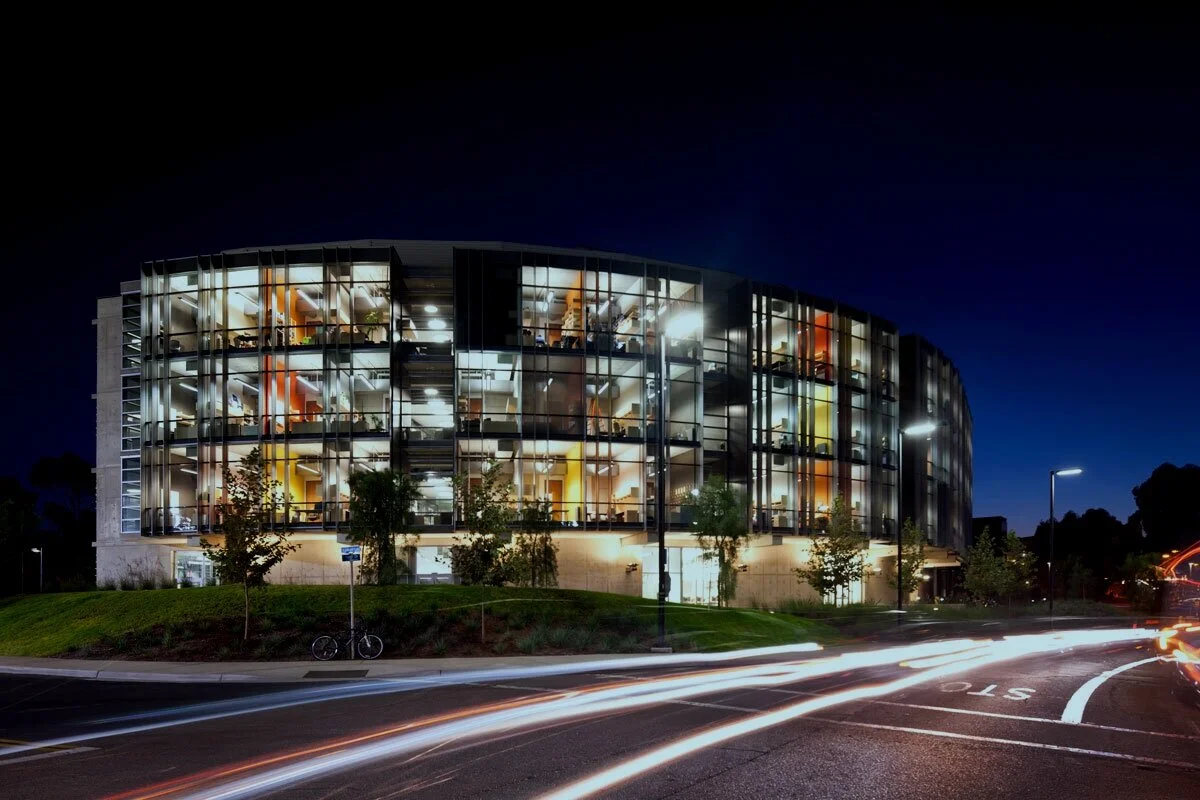
UCSD EnVision: Arts & Engineering Maker Studio
Lab Technician & Supervisor
“The EnVision Arts and Engineering Maker Studio at UC San Diego is a hands-on, experiential education facility where visual arts and engineering communities converge. The nearly 3,000 square foot studio provides a wide range of design, fabrication and prototyping tools, both analog and digital.”
3D modeled, printed, & assembled over 40+ DC motor robot controllers to be utilized in undergraduate lab classes across the UCSD MAE department, an upgrade from ones developed over 10 years ago.
Designed and developed a functional remote wireless control system utilizing Arduino software and sensors to control DC motors to improve cable management and mobility in its applied environments.
Facilitated numerous workshops to teach undergraduate students’ hands-on engineering & prototyping skills such as 3D printing, laser cutting, soldering and operating various electronic equipment and tools.
Led classes teaching various 2D/3D design programs such as AutoCAD, Rhino, ZBrush, SolidWorks, Autodesk Inventor & more.
Organized team meetings and served as a liaison between professors, lab managers and undergraduate students to help with class and personal projects.
Supervised the lab space on a weekly basis, assisting students in their prototyping projects as well as overall machine troubleshooting and maintenance.
Testing our design of the newly upgraded robotic controllers to be used for UCSD's Mechanical & Aerospace Engineering undergraduate lab classes.
Malhas Consulting Engineers
Junior Structural Engineer
Malhas Consulting Engineers is a family owned company located in Clairemont Mesa, CA that specializes in structural expertise in community developments & residential housing renovations.
Partnered alongside a professional engineer on analyzing the structural design & integrity of various community developments & residential housing renovations utilizing SAP 2000
Developed, reviewed & verified floor plans, structural engineering designs & section details utilizing AutoCAD
Coordinated & documented studies & reports during construction site visits & inspections with several engineers, architects & contractors for ongoing projects
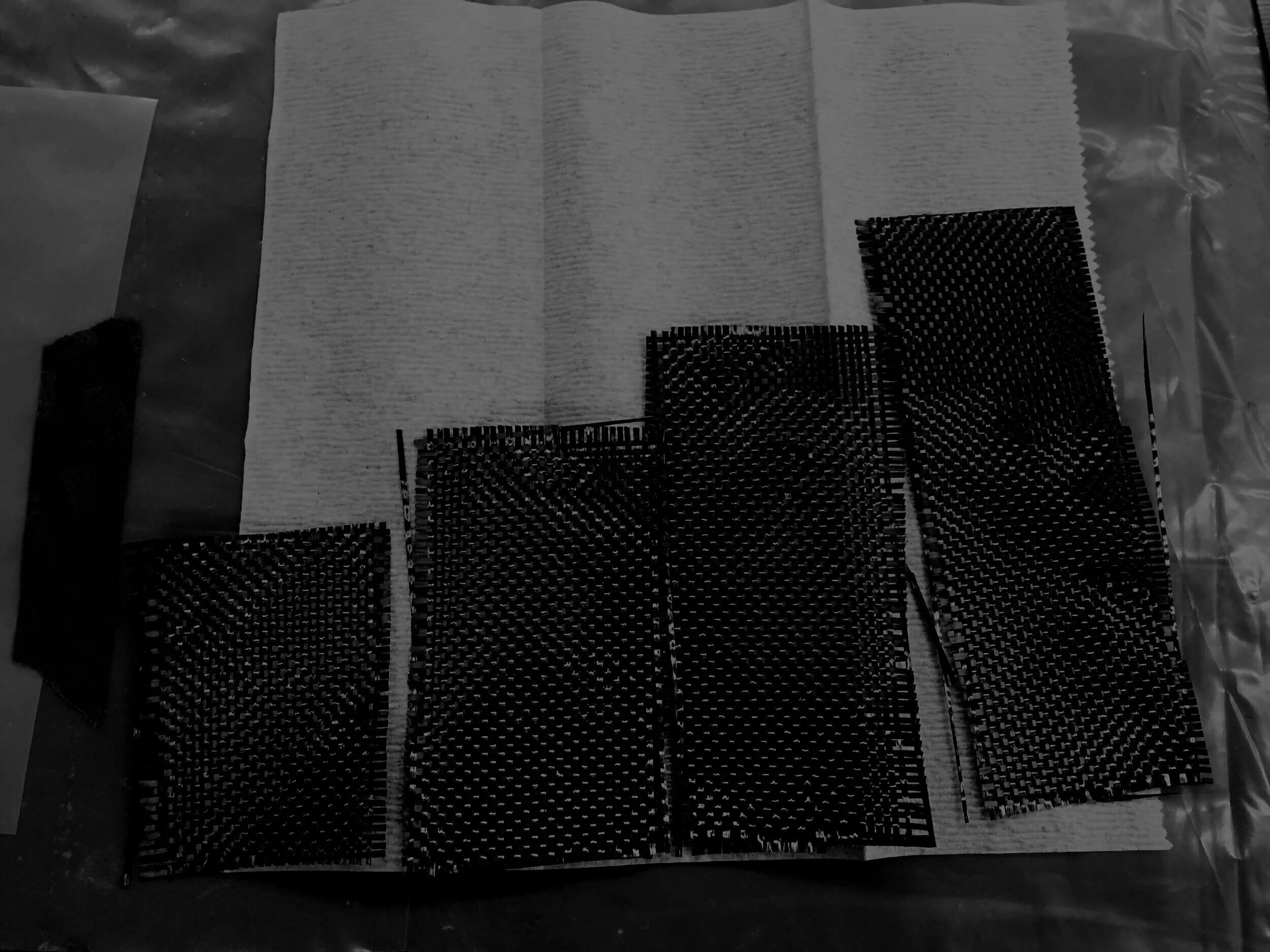
UCSD Senior Design, Aerospace Structures Repair
Development of repair patch for a simulated aluminum panel crack.
The mission of this project was to design a carbon-epoxy repair patch for an aluminum panel with a 2-inch crack in the middle. The goal is to ensure that the repaired specimen is able to withstand at least 80% of the un-damaged aluminum panel strength of 54.4 ksi. Additionally, the repair patch’s smallest step size must not be shorter than 50 times the thickness of the repaired panel (commercial aircraft repair specification).
Utilizing the step-lap Volkersen Model, our team developed MATLAB code to run design iterations with various parameters to finalize our final repair patch approach
We then utilized AutoCAD to draw out our carbon fiber cutout designs to efficiently request the least amount of needed materials to minimize waste
During the manufacturing process we used several techniques such as a sol-gel process, wet lay-ups and vacuum bag curing
In order to hit a certain performance index we also predetermined the expected failure scenario along with the different types of failures associated per load case
Testing our final design of our carbon fiber epoxy composite repair patch on the provided aluminum panel with a 2 inch crack. As you can see the repair patch itself showed no sign of failure. Once the load reached the aluminum's ultimate stress, the panel fractured near the end-tabs and not at the initial crack.

UCSD Senior Design, Advanced Composite Armor
Development of a lightweight custom fit composite armor that must be able to withstand given loads.
Our goal was to create a lightweight, custom fit armor able to withstand strong, but not deadly, forces for the safety of those who have pledged to serve and protect. The armor is designed to be able to fend off shrapnel while also containing emphasized support for the chest region.
Utilizing our knowledge in composite design we wrote a MATLAB code to run various layup combinations to simulate impacts of the given load case to determine our final designed chest plate as the following: [0 -45 45 90 45 -45 0]S
We fabricated the chest plate using carbon fiber prepreg for its lightweight but high strength material properties
Our manufacturing process consisted of a custom fit mold construction, woven glass fiber wet layup, prepreg carbon fiber chest plate integration & a complex vacuum bagging procedure to cure the entire armor piece into one
After load testing, delamination occurred near the chest plate but nonetheless there was minimal surface damage & overall safety was achieved.
After completing the entire wet lay-up process of the composite body armor, we then went through a rigorous vacuum bagging procedure to cure the entire piece.
Final load testing on our final composite design chest plate, that is to be placed in the heart region of our body armor.
Final load testing on our final completed composite body armor.